Meet the new batteries unlocking cheaper electric vehicles
A planned factory marks a major milestone in the US for new batteries that enable lower-cost, longer-lasting EVs.
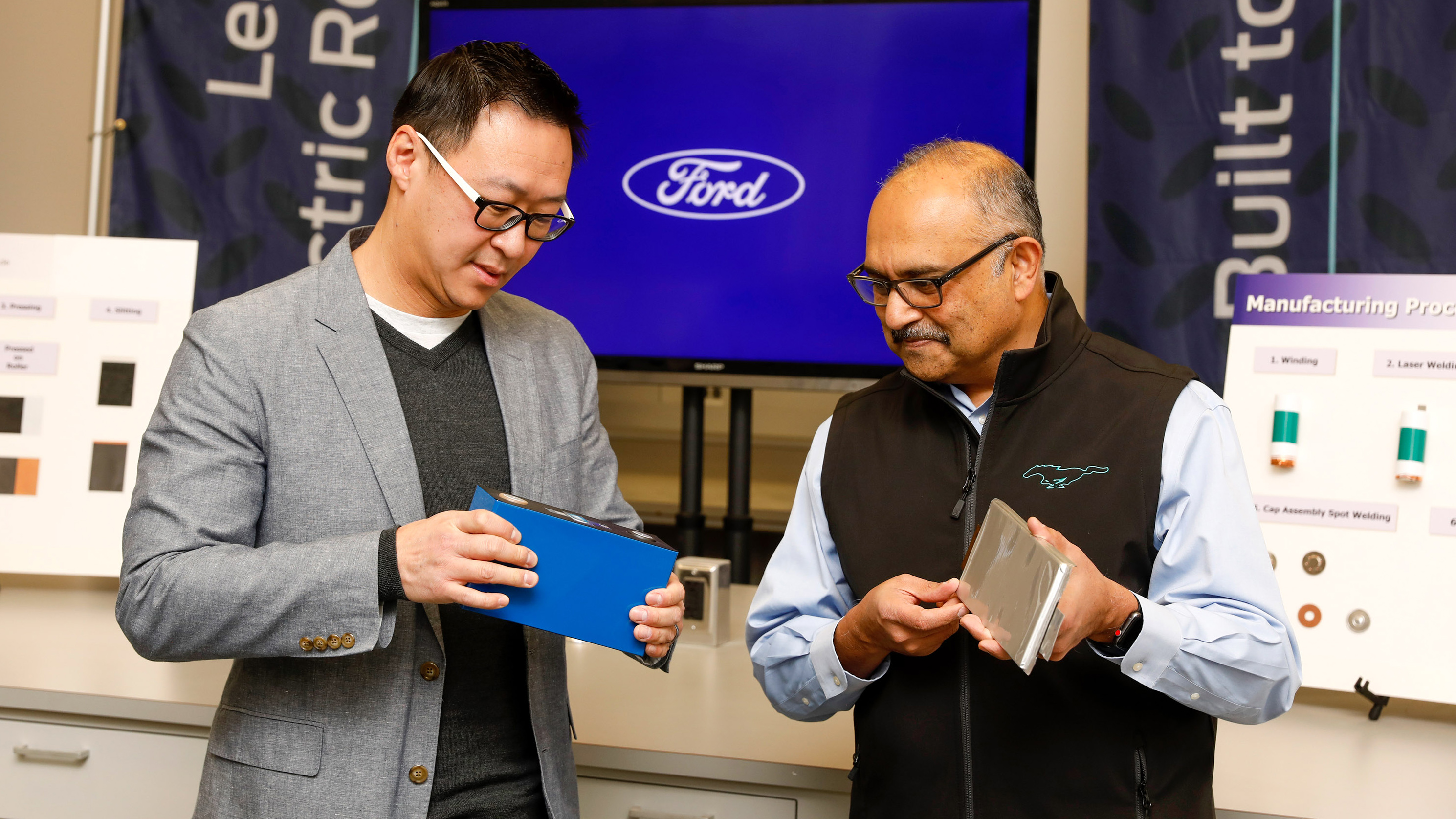
New batteries are coming to America.
This week, Ford announced plans for a new factory in Michigan that will produce lithium iron phosphate batteries for its electric vehicles. The plant, expected to cost $3.5 billion and begin production in 2026, would be the first to make these batteries in the US.
“This is a big deal,” said Michigan governor Gretchen Whitmer in a press conference unveiling plans for the factory. Expanding battery options will allow Ford to “build more EVs faster, and ultimately make them more affordable,” said Bill Ford, Ford’s executive chair.
Also known as lithium ferrous phosphate (LFP) batteries, the type to be produced at the new plant are a lower-cost alternative to the nickel- and cobalt-containing batteries used in most electric vehicles in the US and Europe today. While the technology has grown in popularity in China, Ford’s factory, developed in partnership with the Chinese battery giant CATL, marks a milestone in the West. By cutting costs while also boosting charging speed and extending lifetime, LFP batteries could help expand EV options for drivers.
Lithium-ion batteries all contain lithium, which helps store charge in a part of the battery called the cathode. But lithium doesn’t do this job alone: it’s joined in the cathode by a supporting cast of other materials.
The most common kind of cathode used in vehicles today contains nickel, manganese, and cobalt in addition to lithium. Some automakers, like Tesla, use another cathode chemistry made with nickel, cobalt, and aluminum. Both these cathode types have risen to prominence in part because they have high energy density, meaning the batteries will be smaller and lighter than others that can store the same amount of energy.
While those two used to be the default choices for cathodes in EV batteries, lithium iron phosphate, an older chemistry, has seen a comeback in the past few years, largely driven by huge growth in China.
These iron-containing batteries tend to be about 20% cheaper than other lithium-ion batteries with the same capacity today. This is partly because LFP doesn’t contain cobalt or nickel, expensive metals that have seen huge price swings in recent years. Battery makers are also working to reduce cobalt content because mining the metal has been tied to particularly harmful working conditions.
Making cathodes without cobalt and nickel could help automakers cut costs, and some have already begun to shift battery chemistry used in vehicles sold in the US. Tesla imports LFP cells from China today for some models, including its Model 3. Ford previously announced that it would start using the technology in its Mach-E in 2023 and in the F-150 Lightning in 2024.
With its newly announced factory, Ford would become the first automaker to produce LFP batteries in the US. The new facility, which will use technology from CATL, could help kick-start LFP production in the US more broadly. “It’s a pivotal point for the North American manufacturing landscape,” says Evelina Stoikou, a battery technology analyst at BloombergNEF, an energy-focused research firm.
Several smaller LFP production facilities could also come online around the same time as the Ford plant.
In October 2022, the US federal government announced a nearly $200 million investment to help a company called ICL-IP America build a factory in Missouri. The plant will make material for LFP cathodes, which will then be used to make batteries. It should begin production in 2025.
Meanwhile, a Utah-based company called American Battery Factory is planning a production facility for LFP batteries in Tucson, Arizona. That facility is expected to cost about $1.2 billion and should come online in 2026.
While the increasing availability of alternative battery chemistries could significantly expand options for automakers and drivers, LFP probably won’t fully replace other technologies. “It’s not the holy grail for batteries,” Stoikou says.
LFP batteries are cheaper than other chemistries and can have a longer lifetime, but they also tend to be heavier and bulkier. That can be a problem for vehicles, because if a battery is heavier, it will take more energy to cart around, limiting range. And larger batteries could take up space for seating or cargo.
Drivers in the US and Europe tend to prefer bigger vehicles with longer range. That makes it necessary to pack more energy into a constrained space, so LFP might never dominate in the West as it has in China, Stoikou says.
LFP growth will likely level off after this year, stabilizing at about 40% of the global battery market for EVs, Stoikou says. And looking ahead, we’ll likely soon see other, newer chemistries making their way into cars.
Adding manganese to iron-containing batteries could boost efficiencies while keeping costs low. Automakers could move away from lithium-ion chemistries altogether, instead shifting to solid-state lithium-metal batteries, which could have even higher energy density. And EVs might not even rely on lithium in the future, since sodium-ion batteries could offer a cheaper option down the road.
Each of those chemical combinations might be key to transportation in the future. It's LFP's moment now, but there are plenty of others just behind it.
Deep Dive
Climate change and energy
What’s coming next for fusion research
A year ago, scientists generated net energy with a fusion reactor. This is what’s happened since then.
Is this the most energy-efficient way to build homes?
Airtight and super-insulated, a passive house uses around 90% less energy.
The University of California has all but dropped carbon offsets—and thinks you should, too
It uncovered systemic problems with offset markets and recommended that the public university system focus on cutting its direct emissions instead.
Super-efficient solar cells: 10 Breakthrough Technologies 2024
Solar cells that combine traditional silicon with cutting-edge perovskites could push the efficiency of solar panels to new heights.
Stay connected
Get the latest updates from
MIT Technology Review
Discover special offers, top stories, upcoming events, and more.